Why a proactive trip hazard program makes so much sense
Like any car, boat or home, every facility has assets that require maintenance. Items such as plumbing, lighting, fire safety, landscaping, signage or pathways plus many others. For these assets to remain in top condition, an adequate proactive management approach to maintenance is needed.
A good analogy is wood trim paint on the exterior of a building will allow water to penetrate the wood, leading to cracking, splitting, and decay. Failing to inspect the trim on a regular basis and stretching the paint cycle out several years may save some money today, but it will only allow more damage to take place. Eventually, the damage will require that the wood be replaced at significant expense.
The same thinking applies to concrete surfaces and trip hazards. Maintaining trip hazards year on year removes hazards as they appear for minimal expense. Failing to inspect footpaths and external surfaces frequently means trip hazards can get so big that a simple maintenance repair is not realistic and the only option is replacement which is not only more disruptive, but very expensive. Oh and not friendly for the environment.
Inadequate funding is the most often cited reason for deferring maintenance. However, studies show that on average, for every dollar "saved" by deferring maintenance, there comes a $4 increase in future capital renewal costs. Those are the direct costs for that specific asset. There are additional indirect costs that may have an even larger impact. Over the life of that asset, those additional costs may total more than 15 times what would have been spent on proactive managed maintenance had it not been deferred.
Specifically, in regards to works we do (concrete trip hazard management), we typically see two maintenance approaches:
- Reactive
- Proactive
So what exactly is proactive and reactive maintenance and what are common real world examples we have seen over the years in regards to external surface trip hazard management?
REACTIVE MAINTENANCE:
What is it? Reactive maintenance is when the asset picks the time when it needs urgent service or total replacement and is a bigger problem than it needs to be outside of your direct control
In relation to concrete trip hazards: All too often facilities wait for a trip hazard to become so big or for a trip and fall incident to occur before doing something about it. We get hundreds of “reactive” requests a year to urgently repair a trip hazard after an incident has occurred. Not ideal for the victim of the fall and not ideal for the facility managers as the work is unscheduled, which can lead to delays to action, temporary closure of pathways and extended inconvenience to other users.. A recent example was when an elderly resident at a NSW aged care facility tripped on a raised concrete footpath and ended up in hospital with multiple broken bones where the facility manager then demanded a repair the following day. Sadly this isn’t an isolated example.
Advantages:
- Minimal short term cost savings
Disadvantages:
- Significant deferred costs
- Unplanned call out fee’s/ emergency repairs
- Large liability exposure
- High chance of trip and fall incidents
- Reduced service life of concrete assets
- Large disruption
- Stress
PROACTIVE MAINTENANCE:
What is it? Put simply, proactive maintenance is performing the necessary task when needed
In relation to concrete trip hazards: Ongoing ground movement, weather events, change of seasons and growing tree roots are knowns’ that contribute to trip hazards being inevitable. We can’t control those factors but what can be controlled is implementing a routine and programmed approach to mitigate trip hazards. ie: being proactive. A proven proactive approach is through annual trip hazard inspections (identify), reports (document) and repairs (eliminate). This is our preferred approach that delivers outstanding stress free results for all of our clients.
Typically the first year of implementing a proactive trip hazard approach is the most costly due to the higher volume and size of hazards. However if implemented annually, over 80% of the time the cost reduces year on year. The below table summarises this typical trend from one of our aged care clients sites:

Not one site we work with on a proactive and annual basis have reported a trip and fall incident.
Advantages:
- Safer sites
- Greatly reduced liability
- Less trip & falls
- Small maintenance expenditure especially compared to reactive repairs & replacement works required when maintenance is neglected
- Increased service life of concrete assets
- Proactive program run by trip hazard specialists
- Peace of mind ☺
Disadvantages:
- None. If you can think of any let me know!
SUMMARY:
Deferring maintenance on concrete and footpath assets can cause harm to residents, employees or visitors while also costing much more than a programmed approach.
We get it, there are hundred’s even thousand’s of repair and maintenance items that need attention and there are only so many hours in the day and dollars in the budget to action these. Hopefully this article will help assist you with presenting a case for why footpath trip hazard management is essential for your facility/ site. If you need to discuss a proactive trip hazard management plan and budget or require more data or case studies to strengthen your case, feel free to reach out to me and I would be more than happy to help.
Contact me HERE or on the below details to schedule a time.
Nick Hooper
0406 333 350
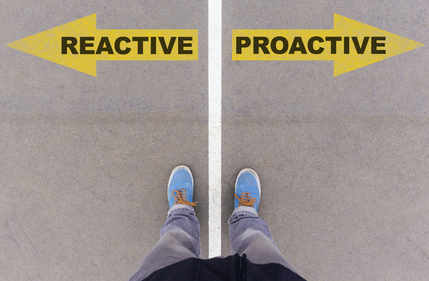
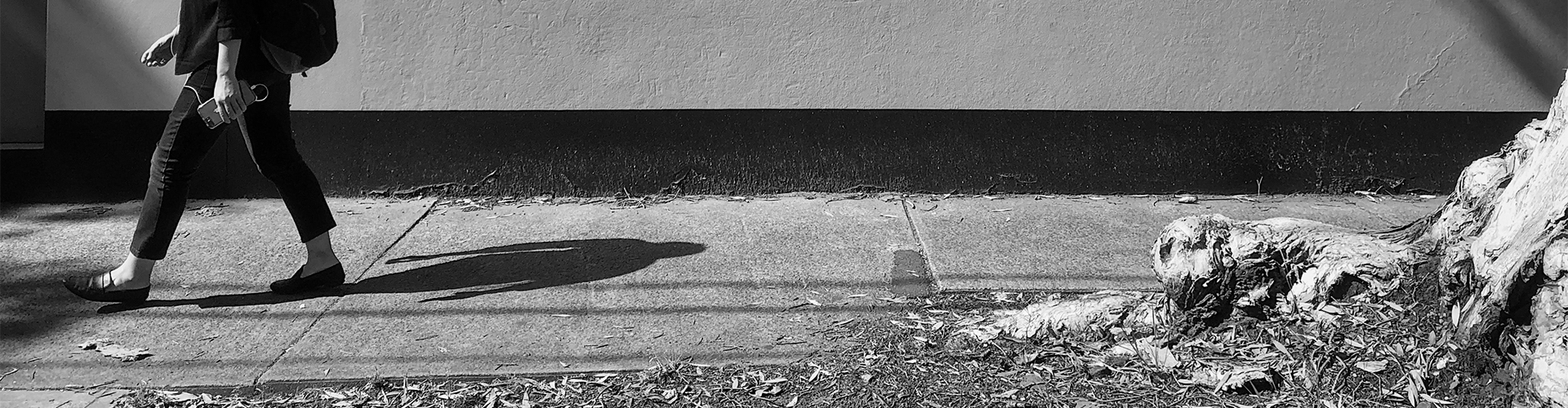
BASED IN MELBOURNE, SYDNEY & BRISBANE AND SERVICING ALL OF AUSTRALIA
If you have questions or would like to a free consultation, please complete the brief form on our contact page.